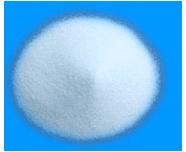
The greatest difficulty encountered in making ultrafine powders is the collection and storage of powders. In addition, the ultrafine powders produced by the wet process require heat treatment, which may cause the specific surface area of ​​the particles to decrease, the activity is reduced, the characteristics of the ultrafine powders are lost, and it is difficult to avoid binding to the carbonyl groups on the surface. Therefore, it is generally preferred to adopt them now. Dry milling.
Nano-powder is a new type of powder metallurgy material and raw material. It is mainly used in high-density magnetic recording materials, conductive materials for thin film integrated circuits, microporous filters, chemical catalysts, automotive reduction catalysts, ultra-fine particle film sensors, and carbon fiber. Vapor-phase nucleation materials, etc.
The nano-powder has high activity, is easy to agglomerate and moisture oxidize, and has poor formability. Therefore, there are still some technical problems to be solved as powder metallurgy raw materials. In addition, nanopowders must have economical manufacturing methods and stable quality as raw materials for powder products. The nano-powder sintering temperature is particularly low (the sintering temperature of the silver powder with a particle size of 20 nm is 60 to 80° C., and the 20-nm nickel powder starts to be welded at 200° C.), once the powdered metallurgical products can be produced industrially using the nano-powders. Breakthrough changes will be made to powder metallurgy technology.
Wall-Mounted Fume Exhaust,Wall-Mounted Fume Exhaust System,Laboratory Wall-Mounted Fume Exhaust,Wall-Mounted Fume Exhaust Hood
NARWILL IMPORT&EXPORT CO.LTD , https://www.narwill.com