Cement is the most basic material in home-installed hard-packs. If it buys fakes, the trouble behind is not a little bit, so it's important to learn to distinguish between true and false cement.
“Seeing, smelling, asking, and cuttingâ€â€”The cements with different standards for cement in the four steps are all different in quality and scope of application. Faced with a wide variety of mixed products, it is difficult for ordinary consumers to accurately identify. The safest way is to choose the products of regular manufacturers.
The first step: "look at" mud known good or bad . First of all, from the appearance of the packaging quality. To see if the use of a damp-proof performance is not easy to damage the laminating woven bags to see if the logo is clear and complete. In general, the cement produced by regular manufacturers should be marked with the following contents: registered trademarks, place of origin, production license number, implementation standards, packaging date, bag net weight, factory number, and cement varieties. However, poor quality cement is often unknown. Second, carefully observe the color of the cement. In general, the normal color of cement should be grayish, and the color is too deep or there may be too much other impurities. The second step: "smell" mud analysis quality. The smell here is not a smell. After all, it is unsafe for cement to be heard by consumers. The “smell†here is “hearingâ€. Listen to the business’s introduction of the ingredients of cement to infer cement quality. At present, some small cement plants in China have used cement mixing materials in excess of cement standards in order to carry out low-priced sales, and have not strictly followed the national standards to match the raw materials. The performance of their products can be imagined. The regular manufacturers are very rigorous in the selection of raw materials for cement. The third step: "ask" the source of mud. It mainly asks cement manufacturers and production processes to see if their “origin†is formal and whether the production process is advanced. At present, the cement products on the building materials decoration market are mostly produced by the small vertical kiln process. Not only the product quality is very unstable, but also the enemies of environmental protection; and some professional large plants adopt the new dry process rotary kiln production and adopt advanced computer technology control. Management can ensure the stability of the cement product quality. The fourth step: "cut" mud known life . This step mainly uses the fingers to give the cement a “pulse†and distinguishes the length of its delivery time. Cement also has a shelf life. In general, the strength of cement that exceeds the delivery date of 30 days will decrease. After three months of storage, the strength of cement decreased by 10%-20%, decreased by 15%-30% after six months, and decreased by 25%-40% after one year. The cement that can be used normally should not be subject to damp and agglomerate, and the high-quality cement should be cement powdered with a finger and feel fine grained. Packing of poor quality cement will result in moisture and agglomeration of the opening inspection. The inferior cement is cemented with fingers and has a rough feel. This indicates that the fineness of the cement is coarse and abnormal, and the strength of the cement is low and its viscosity is poor.
After completing the "four steps" for cement, does this mean that you have already done it? No! After you have selected the right cement, you must use the correct method of use to make these high-quality products. Cement products play their due role. First, pay attention to the reasonable ratio of mortar. For example, it is advisable to select the appropriate proportion of mortar according to the parts used, such as wall-witting, affixing bricks, and affixing wall tiles, and it is advisable to mix the good mortar each time in two hours. Second, the use of special sand mortar for building materials market , in particular to control the quality of sand containing mud, high mud content will reduce the degree of adhesion. Third, the tiles should be fully immersed before use (more than 2 hours) dried , to avoid mortar due to water loss to reduce strength; floor tiles should use dry shop, wall tiles should be wet shop. Fourth, the mortar should be mixed evenly . It is recommended to use it within 2 hours and 30 minutes after mixing the mortar.
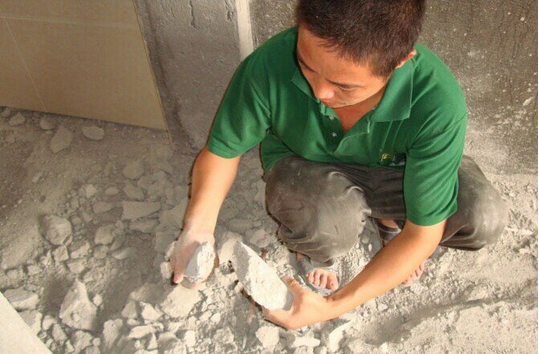
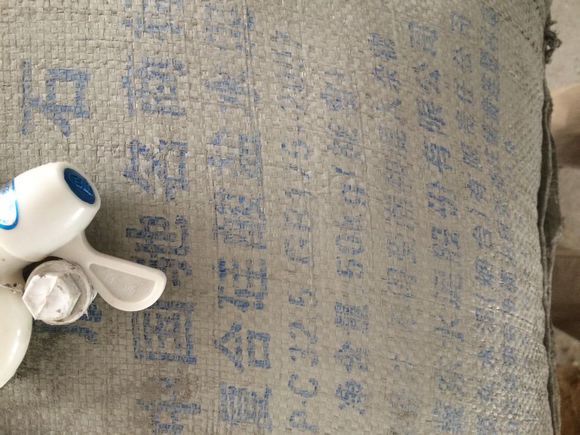
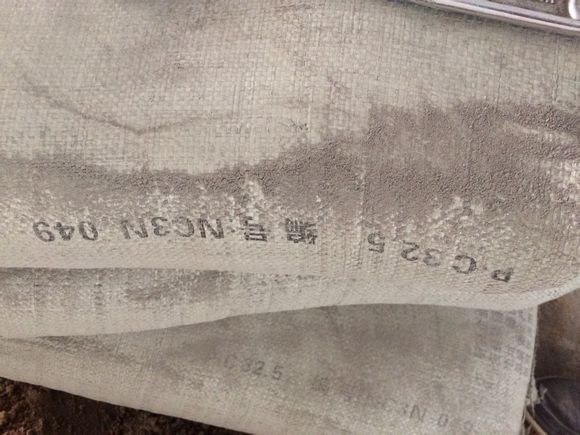
Yellow sand cement cement
Flanged Carbon Steel Ball Valve
Flanged Carbon Steel Ball Valve,Mild Steel Ball Valve,Carbon Steel Flanged Ball Valve,Carbon Steel Socket Weld Ball Valve
Zhejiang Chenxiang import and export trade Co., Ltd , https://www.chenxiang-valve.com