In the past ten years, the automobile industry has developed rapidly. In 2012, there were about 68 million new registered vehicles in the world, including more than 19.3 million vehicles produced and sold in China, which has been the world's number one for four consecutive years. Due to the protection of the environment and energy, the world has put forward higher requirements for the automotive industry in terms of energy conservation and emission reduction. In order to meet and surpass these new requirements, the four major systems of the car show their brilliance, providing positive energy for energy saving and emission reduction. The body system of one of the four major automobile systems is being studied and discussed as one of the main measures for energy saving and emission reduction while reducing the weight of the vehicle body under the premise of ensuring safety. From the design point of view, how to reduce the number of parts and simplify the structure of the parts in terms of the strength of the body parts; reduce the manufacturing process from the perspective of manufacturing realization and accelerate the manufacturing process. The connection between the body system and other systems of the car is often achieved by the coupling of the nut and the bolt, while the traditional connection between the nut and the body part is mostly achieved by projection welding, and now a body with one or more nut columns The piece is being gradually used. The figure below shows the front bracket rear bracket reinforcement of a certain model.
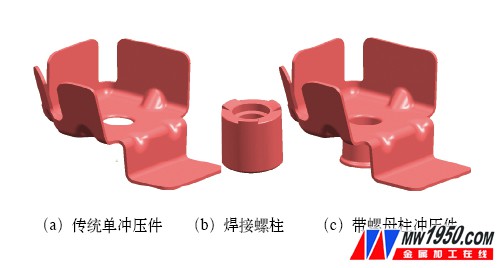
Front suspension of the rear bracket of a certain model
Nut column parts features
(1) Reduction in the number of parts The small assembly consisting of at least two parts should be simplified into a single nut-column stamping, reducing the part level and the number of parts.
(2) Simplified production process The nut is no longer produced separately, and the projection welding process of connecting the nut to the stamping part is omitted.
(3) Technical and quality requirements are guaranteed. The nut column stamping parts are integrated. The verticality requirements and joint strength requirements of the nuts and parts are guaranteed at one time, which greatly reduces the quality risk caused by quality problems such as nut cold welding.
(4) Cost reduction The structure of the nut column stamping part determines the realization process compared with the traditional process, eliminating the energy consumption and material loss required for the separate production of the nut, eliminating the energy consumption and material loss required for the welding connection, eliminating the need for Logistics costs required for nut transportation and distribution. At the same time, it also reduces the labor and management costs caused by the prevention of quality risks and processing quality problems in the traditional structure.
(5) Increased technical difficulty of parts realization The nut column mainly plays the role of support, passage or connection, so most of the nut columns have load bearing requirements. In general, the wall thickness of the nut column exceeds the wall thickness of the formed sheet, so there is a requirement for thickening of the steel sheet during the forming process. Thickening is difficult to achieve in the stamping process. According to different nut column requirements, if you use a traditional stamping process to achieve, you often need 5 to 15, or even more processes.
Technical realization of nut column stamping parts
If the nut column stamping part is realized by the traditional stamping single-step process, the manufacturing cost is very high, but with the effective application of the nut column thickening continuous drawing process, the problem of excessive manufacturing cost is solved. The nut column thickening continuous drawing process refers to a single nut column or a nut column plus the overall shape of the part in the same sub-mold, which is divided into different steps. There are 20 or more steps in a set of molds that are produced using high-speed punching machines. According to the degree of mastery of technology, the number of parts produced per minute is 2 to 4 times that of conventional processes, thus greatly improving the parts. Production efficiency reduces manufacturing costs.
Under normal circumstances, the higher the height of the nut column of the nut column stamping, the more the number of nut columns in the same part, the smaller the spacing between the nut columns, the higher the thickness ratio of the nut wall thickness, the smaller the diameter of the nut column, the difficulty of forming. The bigger. With its advanced mold design and manufacturing technology, the German nut column stamping forming technology is the most mature. According to the data, in the matching system of General Motors (GM) in North America, a stamping company in Germany uses a 2.0mm thick steel material through a nut column thickening continuous drawing process, and the distance between the same plane is only about 180mm, achieving two The mass production of the nut column is about 15mm in diameter and about 38mm in height, and the material thickening ratio of the nut part is more than 1.8 times. There is still a certain gap between the domestic nut column stamping technology and Germany, but in recent years there has been a very big breakthrough.
The following is through the localization project of our company's nut column stamping parts (formerly imported from Germany), which explains the realization process of the nut column stamping parts. Through the nut column thickening continuous drawing process combined with the traditional single-step processing, the nut column stamping parts with higher difficulty are realized. .
1. Part technical requirements
The maximum load of the nut is 85kN, the maximum compression of the nut height is 0.13mm, the thickness of the steel is 1.95mm, the substrate is CR3, the thickness of the zinc layer is galvanized plate of HD60G 60GU, the wall thickness of the nut column is 3.0mm, that is, the nut column is required from 1.95mm. Thickened to 3.0mm (thickness ratio is 1.54 times). This product is a left and right piece, and the bicycle production is 200,000 to 300,000 sets per year.
2. Manufacturing process design
According to the company's existing equipment and technical status, the part manufacturing process is realized by the nut column thickening continuous stretching process, combined with the traditional single process processing. The nut column is realized by a nut column thickening continuous drawing process, and then the nut column size, load correction and other dimensions and shape requirements of the part other than the nut column are realized by the conventional single-step manufacturing method.
The advantage of the nut column thickening continuous drawing process to achieve the nut column is that the entire forming process of the product is completed in a pair of molds, which overcomes the inconvenience and cumulative error caused by multiple positioning with a simple mold; the nut column is continuously stretched. The characteristics of the process structure are that the process is connected by the material belt and pushed by the feeder; it consists of multiple steps; each step completes different processing; the punching machine completes a series of different stamping processes in one stroke; automatic output; production efficiency Higher.
The difficulty of the nut column thickening continuous drawing process and the key technologies are: the progressive die structure is complex, the work steps are more, the nut column realizes the cumulative size of the stretching and forming of each process, and finally determines the height and diameter of the nut. In the stretch forming, the stretch ratio of each process is the key dimension that determines the next stretch. In the continuous forming, the stretch insert does not allow a large area of ​​wear, so the TD surface is required for the stretch insert. Ultra high alloy plating.
Based on the above analysis, this localized part was designed to consist of 11 processes for the entire manufacturing process. The parts produced in this process are qualified by the inspection tool and the three-coordinate measurement to verify the size of the parts. Through the fatigue test of the whole vehicle, the performance is verified to meet the requirements. At present, mass production of localized projects has been realized.
The entire manufacturing process is:
(1) Continuous production of nut column to realize the production of blank with nut column Using the 600t grade punching machine of the machine tool, the production efficiency is 15~20 pieces/min. The mold size is 674 mm × 3180 mm × 800 mm, and the coil size is 1.95 mm × 370 mm × L. There are 17 steps in the mold, in which five steps are punched, 11 steps are stretched, and one step is cut. The billet produced by the nut column continuous drawing process has a nut column with a diameter of 26 mm and a height of 38 mm.
(2) Two piers are squeezed using a 160t small punching device to achieve a nut column diameter of 26mm and a height of 30mm.
(3) Punching Using a 110t small punching device, the nut column has a diameter of 19.8 mm and a height of 30 mm.
(4) Playing Huff Using a 160t small punching device, the diameter of the nut column is 19.8mm and the height is 27mm.
(5) Punching The final size of the nut column is achieved by using a 110t small punching device with a diameter of 20.1mm and a height of 27mm.
Finally, through the shape of blanking, bending, cutting, marking, forming, chamfering (the first four steps are used 110t small punching equipment, chamfering with drilling machine) five steps to achieve the shape of the part.
Application of nut column stamping parts in automobile body system
The emergence of high-difficult nut-column stamping parts technology (especially the one-shot forming nut-column continuous-die process) is becoming more and more widely used because it meets the requirements of the development trend of energy saving and emission reduction of the body system. Since 2007, our company has more than 10 similar parts for various OEMs. The parts shown in the drawings have been approved by the OEM in June 2013 and have been mass-produced. According to the forecast, this localization project will bring the cost reduction of more than one million yuan per year to the enterprise, which fully proves that technological innovation is the main source of cost reduction and efficiency increase.
Leader Hardware provides all ranges of glass hardware for commercial use and residential use, e.g. glass hinges, glass clamps, sliding door systems, and so on. We always purchase high-quality raw materials to ensure the anti-rusting and corrosion resistance performance of our products. All of our products are available for various surface finishes, like satin finish, polish finish, matt black, and so on. With our own R&D team, we provide OEM and ODM services.
Glass Door Hardware,Glass Door Closer,Cabinet Glass Door Hinges,Square Edge Clamps,Glass-to-Glass Clamps, Glass-to-Wall Clamps
Leader Hardware Manufacturer Limited , https://www.leaderhardwarecn.com