In large mold processing, in order to obtain the highest possible surface quality, we need to select the right machine tool and configure the necessary tools. Only in this way can we reduce the EDM's subsequent processing time and the manual grinding time of the fitter. With the rapid development of the automotive industry, the demand for various large and highly decorative molds for automobiles is rapidly increasing. For example, automotive dashboards, designers are constantly increasing the size and complexity of such mold products. Therefore, the production of various large molds has become a new field for many processing companies to seek opportunities for global competition. However, it is not an easy task to enter this field. Under the backward processing technology, the machine feed rate is slow, the operator needs to perform multiple debugging and clamping on the workpiece, and it takes several hours of manual polishing, so the processing cycle is very long. Therefore, more advanced processing techniques must be sought to make the processing of large molds as easy as machining small molds.
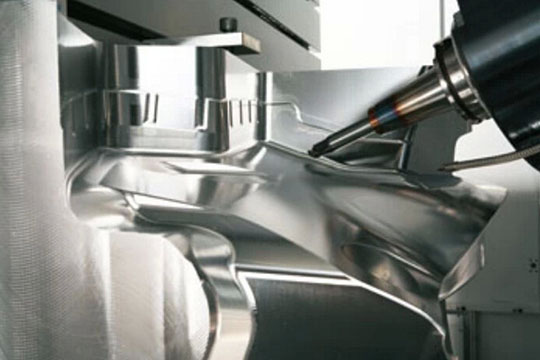
The main problems in large mold processing:
1. Huge size and weight
When processing large molds, how to deal with their own huge size and weight is a major challenge for processing companies. The processing of large molds often requires a large amount of labor, special equipment and multiple debugging and clamping, and the processing accuracy is also affected by many potential factors and is not easy to guarantee.
2. Acquisition cost problem
  The biggest cost directly related to the processing and production of various large-scale molds is the purchase cost of the machine tool. Machine tools capable of producing large molds are quite expensive, especially in complex process arrangements where multiple machines are required to complete the entire process from mold roughing to finishing. Such early high input costs are also the biggest obstacle for many companies to enter this market. From this, we can see that if the roughing and finishing of large molds can be realized on a suitable machine tool, even if it is only necessary to debug the clamping, many problems will be solved and the machining accuracy can be guaranteed.
Large mold processing center
Considering the general machining accuracy of large machine tools and the problem of commissioning and clamping, we must explore some of the design features necessary for large mold machining centers.
1. Cast iron bed structure, machine tool spindle has heat dissipation function
Cast iron materials have high rigidity and heat dissipation properties and are therefore the most stable material for manufacturing machine tool structural parts. For any machine for milling large parts, you first need to have a very strong cast iron structure and be equipped with a heat sink.
As far as the spindle of the machine is concerned, it must use built-in cooling technology to cool the spindle from the outside of the bearing to ensure that the spindle itself will not be burned out or will not be lost due to thermal expansion during long processing. These factors are very important because the processing of large molds takes a long time, and under heavy cutting conditions, this increases the heat and stress of the mold. Therefore, the structural components of the machine tool must have good rigidity and heat dissipation characteristics, which is the premise of processing large-scale high-quality molds. Therefore, it is necessary to minimize the vibration of the machine tool during the machining process and to rapidly diffuse the heat generated during the machining process. Choosing the right machine tool and tool can achieve a win-win cost and cycle.
2. Thermal stability technology
Due to the long processing time, the influence of ambient temperature must also be considered. For example, when machining large molds on a common machine tool, when the ambient temperature changes by 10 °C, it will cause a temperature change of 6 °C on the machine column, causing a 0.07 mm change in the parallelism of the main shaft gusset. Therefore, the design of the machine tool must take into account the effect of the ambient temperature and avoid the ambient temperature affecting the accuracy of the machined part.
3. Speed
For a large mold processing center that can move quickly, the spindle speed of a large mold processing machine should be at least 20000r/min, and the cutting speed of metal should be 762~20000mm/min.
4. Accuracy
Accuracy control always runs through all stages of mold processing. If rough machining and finishing of large molds are required on one machining center, the positioning accuracy and repeatability of the machine must be strictly controlled. The machining center for large molds generally has a positioning accuracy of ±1.5μm and a repeatability of ±1μm. At the same time, its pitch accuracy should be kept within 5μm.
High precision surface machining
4. Feedback resolution
The feedback resolution of the machine itself is very important for detecting the accuracy of the machined parts. With a standard 1 μm feedback resolution, the results usually are not very satisfactory. If the resolution can reach 0.05 μm, there is almost no flaw in the finishing result. Moreover, the machining quality of the surface of the part can be further improved by controlling the resolution of the machine, the scale feedback and the small pitch ball screw.
5. Spindle
The spindles used in large mold machining centers must meet the requirements for roughing, semi-finishing and high-quality finishing, and as a reference standard, the surface finish quality that can be achieved should be controlled at a level of 2 μm. In general, the finishing of the mold closing surface and the parting line is very important, but in the traditional process, many mold manufacturers have to use the manual polishing method to compensate for the problem of insufficient tool processing accuracy. Because the cost of large-scale machine tools is expensive, it is obviously unrealistic to purchase multi-function machine tools for this process.
Horizontal machining center with spindle angle changeable with workpiece
In addition, a reasonable spindle design must maximize the life of the tool so that it can continue to operate with low vibration and low temperature during the machining cycle. For example, when machining automotive dashboard molds on a large mold processing center, such as 16mm CBN insert finishing tools, the processing speed can reach 8m / min, the service life is more than 30h, the processing surface quality can be controlled at 0.336 ~ 3.2μm. It can be seen that, considering the increase of the tool cost when processing a large mold, the use of a specially designed large-scale mold processing machine can not only prolong the service life of the tool, but also can greatly save the cost of processing the tool for each mold.
6. Movable multi-axis machining head
Due to the size and weight limitations of the mold, it usually takes a long time to clamp the workpiece. Therefore, the use of the 3-axis linkage machining center not only reduces the number of debugging and clamping of the workpiece, but also does not affect the machining accuracy of the machine tool, thereby greatly improving the production capacity of the large-scale mold in the workshop.
The movable multi-axis machining head can be used to machine large-sized molds with particularly complicated structures. The machining head designed according to the variable geometry allows 3-axis simultaneous machining. The workpiece can be milled only once, and the machining cavity can be deep. Molds and cooling holes, as well as many other geometrically complex parts that are machined. For example, when the spindle is tilted at an optimum angle, the proximity of the machining head to the milling point can be improved, so that the processing of the inclined hole can be completed by using the multi-axis machining head.
In addition, since the multi-axis machining head processes the surface of the workpiece, the radius of the cutter is used instead of the tip of the cutter, so that the surface roughness can be improved.
7. Chip management
A large amount of chips are generated during metal cutting. If it is not removed in time, it will inevitably lead to secondary cutting and temperature rise of the structural parts of the machine tool or the surface of the workpiece. The large mold machining center usually has 18 chip evacuation holes under the workbench, which can reliably remove the chips regardless of where the table is moved. The machine has four built-in hinged chip conveyors that deliver chips to the front of the machine at high speeds.
8. High pressure coolant
High pressure coolant plays a very important role in large mold processing. For example, when drilling a slant hole with a 2+3 axis machining method, a coolant of 1000 psi (1 psi = 6890 Pa) is required to effectively remove chips and achieve higher precision cutting. If there is no such high-pressure coolant, it is necessary to add additional machine tools when machining the inclined holes, which requires secondary loading, which reduces the machining accuracy and increases the cycle cost. According to the above analysis, it can be seen that the simple processing of large molds requires more and better functions of the machine tool. The new MCC2516VG3 shaft horizontal machining center developed by Makino has a spindle speed of 15000r/min and adopts the "shaft cooling" method and the "bearing internal pressure lubrication" function to ensure timely and effective cooling of the spindle and its associated bearings. . In addition, the main shaft can move not only in the X-axis in the lateral direction, the Y-axis in the vertical direction, and the Z-axis in the front-rear direction, but also in the A-axis and the C-axis. Thanks to the two indexing functions, it not only reduces the amount of adjustment work, but also cuts complex workpieces such as bumpers, instrument panels and car headlight lenses.
Weigh 50-300kg Electronic Scales
Weigh 50-300Kg Electronic Scales,Jewelry Scale,Hanging Grocery Scale,Hanging Measuring Scales
Shanghai Liuyuan Trading Co. , Ltd. , https://www.ly-weighing.com